Die Casting Process Introduction: From Principles to Applications
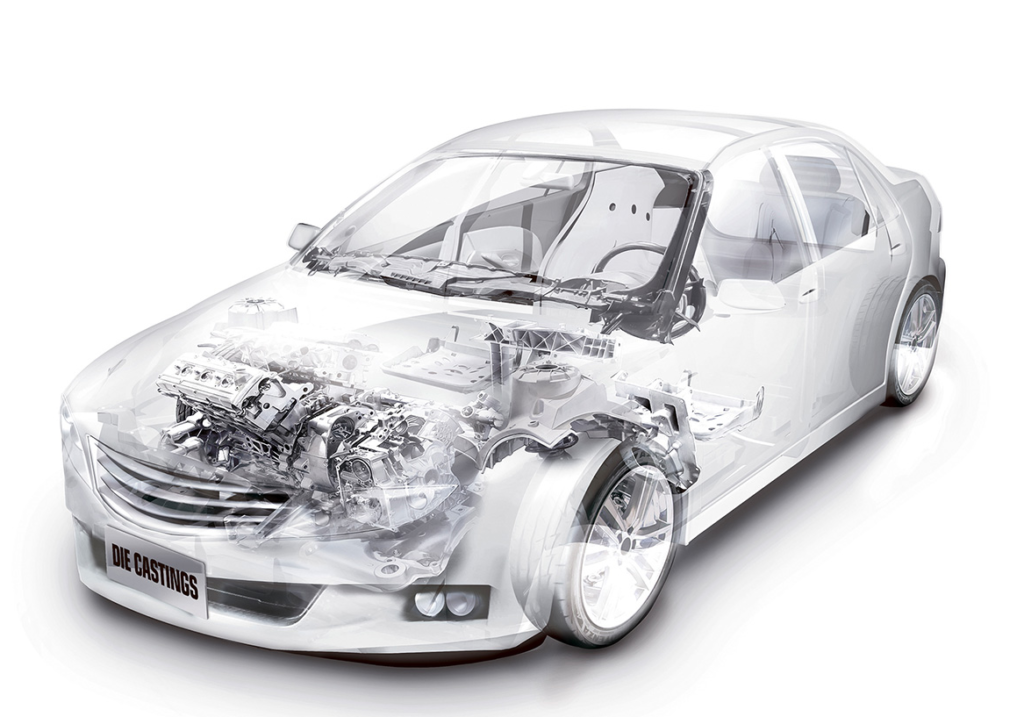
Introduction:
Die casting is a versatile manufacturing process that allows for the production of precise and complex metal parts. At its core, die casting involves injecting molten metal into a mold cavity under high pressure, where it solidifies to form the desired shape
The production of die-casting parts in China has been continuously increasing in recent years. For example, the total production of die-casting parts in China in 2023 was 4.62 million tons, an increase of 3% compared to 2022. In 2024, the total production of castings in China reached 54.05 million tons, a year-on-year increase of 4%. Among them, the production of automotive castings was 15.4 million tons, accounting for 28.5%.
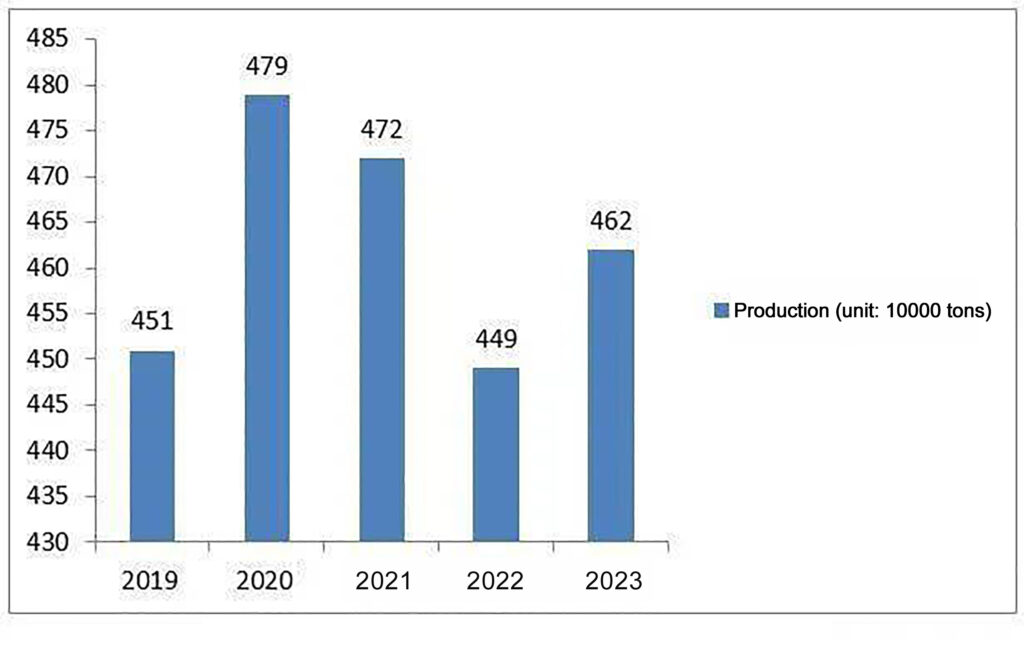
1、Understanding the Basics of Die Casting: Principles and Processes Explained
1.1、Principles of Die Casting
Die casting begins with the creation of a mold, also known as a die. This mold is typically made from durable materials such as steel or aluminum and is designed to withstand the high temperatures and pressures of the die casting process. The mold is carefully crafted to include the negative shape of the desired part, allowing for the precise replication of intricate details.
1.2、Process Overview
Once the mold is prepared, the next step is metal preparation. The chosen metal, typically an alloy such as aluminum, magnesium, or zinc, is melted in a furnace and then poured into a ladle. From there, the molten metal is injected into the mold cavity at high pressure using a specialized die casting machine.
1.3、Solidification and Cooling
As the molten metal fills the mold cavity, it begins to cool and solidify. This process is known as solidification, and it is crucial for achieving the desired part shape and properties. Proper cooling and solidification ensure that the final part has the necessary strength, surface finish, and dimensional accuracy.
1.4、Part Ejection and Finishing
After the metal has fully solidified, the mold is opened, and the newly formed part is ejected. The part may undergo additional finishing processes, such as trimming excess material or surface treatments, to achieve the desired final appearance and properties.
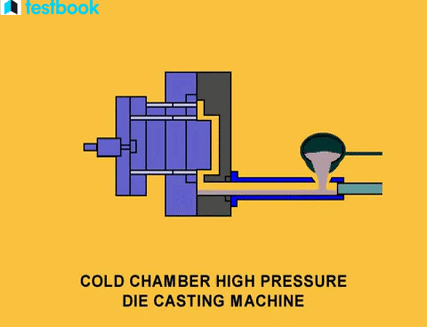
2、Common Die Casting Equipment and Tools Introduction
Die casting relies on a combination of equipment and tools to transform molten metal into intricate and precise parts. Understanding the role and characteristics of each component is essential for ensuring successful die casting operations in automotive parts manufacturing.
2.1、Die Casting Machines
Die casting machines are the backbone of the die casting process, responsible for injecting molten metal into molds under high pressure. These machines come in various sizes and configurations, ranging from small, high-speed machines for small parts to large, high-pressure machines for larger components.
2.2、Die casting ’s Molds
Molds, also known as dies, are custom-made tools used to shape the molten metal into the desired form. They are typically made from durable materials such as steel or aluminum and are precision-engineered to withstand the high temperatures and pressures of the die casting process. Molds play a crucial role in determining the final shape and quality of the cast parts.
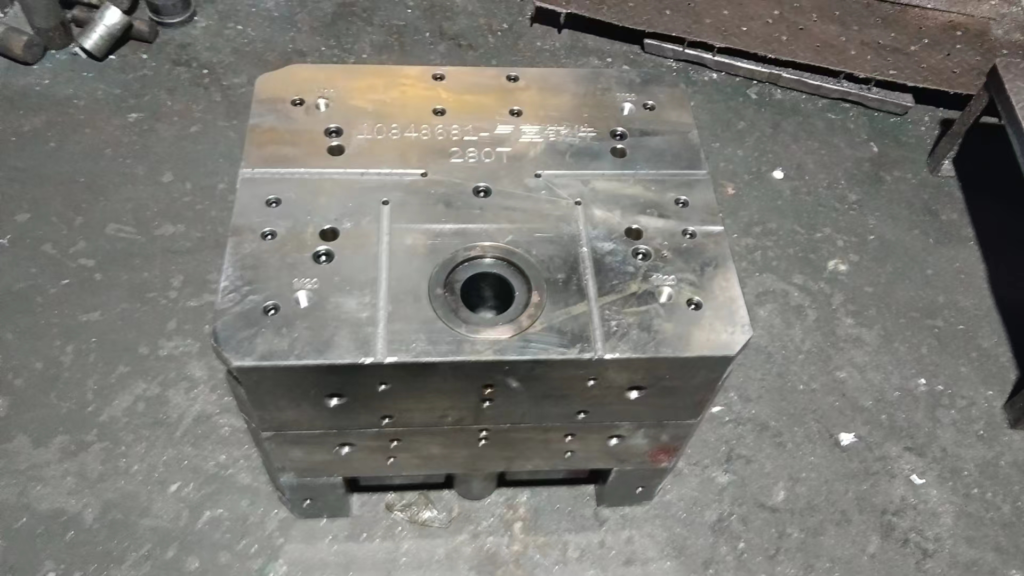
2.3、Furnaces
Furnaces are used to melt the metal alloys used in the die casting process. These furnaces are designed to reach high temperatures quickly and maintain precise temperature control throughout the casting process. Depending on the size and capacity of the die casting operation, furnaces may vary in size and configuration.
2.4、Other Tools and Equipment
In addition to die casting machines, molds, and furnaces, other tools and equipment are essential for die casting operations. These may include ladles for transferring molten metal, trimming presses for removing excess material from cast parts, and cooling systems for maintaining optimal casting temperatures.
3、Die Casting Material Selection and Characteristics Analysis
The choice of material is crucial in die casting. It directly impacts the performance, durability, and cost-effectiveness of the final automotive parts. Understanding the properties and characteristics of different die casting.Materials is essential for selecting the most suitable option for specific applications.
3.1、Aluminum Alloys
Aluminum alloys are widely used in die casting for automotive.Applications due to their excellent strength-to-weight ratio, corrosion resistance, and thermal conductivity. Some commonly used aluminum alloys for automotive die casting include:
Aluminum 46100 / ADC12 / A383 / Al-Si11Cu3
Aluminum 46500 / A380 / Al-Si8Cu3
These aluminum alloys offer a good balance of strength, ductility, and machinability, making them suitable for a wide range of automotive parts, including engine blocks, transmission cases, and structural components.
3.2、Zinc Alloys
Zinc alloys are another popular choice for automotive die casting due to their excellent casting properties, dimensional stability, and surface finish. Zinc alloys offer high strength and hardness, along with good corrosion resistance and wear resistance. Some commonly used zinc alloys for automotive die casting include:
Zamak 3
Zamak 5
ZA-8
Zinc alloys are often used to produce automotive parts such as brackets, hinges, and decorative trim components.
3.3、Magnesium Alloys
Magnesium alloys offer the highest strength-to-weight ratio of all commonly used die casting materials. Making them ideal for applications where weight reduction is critical. Magnesium alloys also offer good heat dissipation and electromagnetic shielding properties. Some commonly used magnesium alloys for automotive die casting include:
AZ91D
AM60B
AS41B
Magnesium alloys are commonly used in automotive applications such as steering wheels, transmission cases, and structural components.
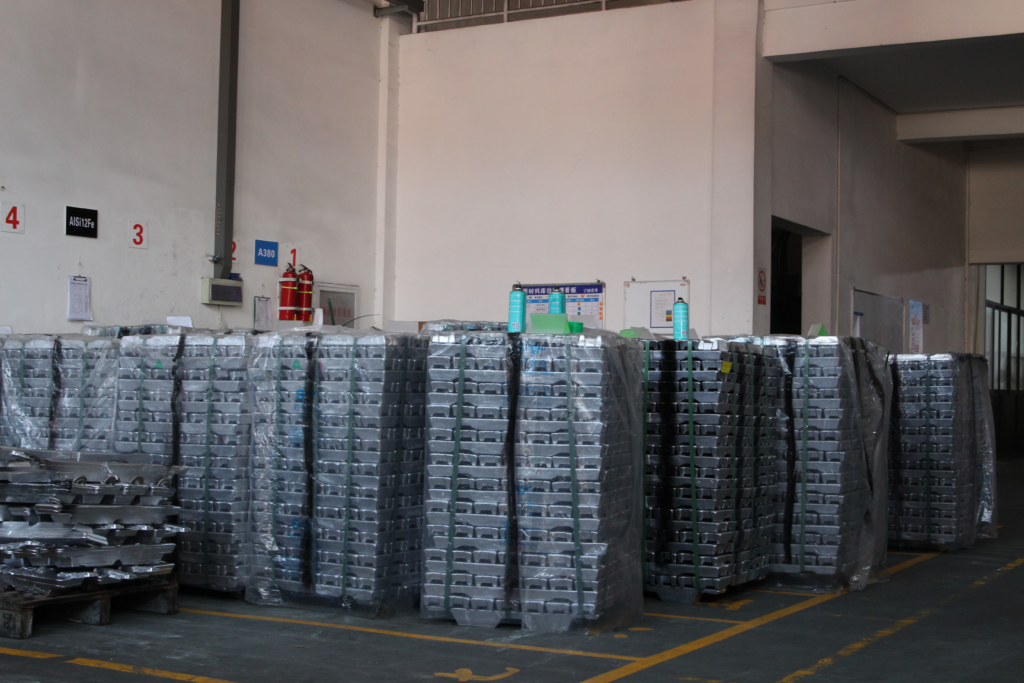
4、Different Types of Die Casting
Die casting techniques vary based on the method used to introduce molten metal into the mold cavity. Hot chamber and cold chamber die casting are two primary methods employed in automotive manufacturing, each with distinct characteristics and applications.
4.1、Hot Chamber Die Casting
Hot chamber die casting, also known as gooseneck casting, involves feeding molten metal into the mold cavity directly from a furnace. This method is suitable for alloys with lower melting points, such as zinc and magnesium. Hot chamber die casting offers advantages like faster cycle times, reduced energy consumption, and simplified operation.
However, it may not be suitable for high-melting-point alloys or parts.Requiring intricate details due to limitations in temperature control and mold durability.
4.2、Cold Chamber Die Casting
Cold chamber die casting involves ladling molten metal into a separate chamber, from which it is then injected into the mold cavity using a plunger. This method is preferred for alloys with higher melting points, such as aluminum and copper. Cold chamber die casting offers greater flexibility in material selection and can accommodate larger and more complex parts. However, it typically requires longer cycle times, higher initial investment in equipment, and may result in higher energy consumption compared to hot chamber die casting.
4.3、Choosing the Right Die Casting Type for Automotive Applications
In the automotive industry, the selection of die casting type depends on various factors. Including the material properties, part complexity, production volume, and quality requirements.
For components requiring high precision, intricate details, or made from high-melting-point alloys like aluminum.cold chamber die casting is often preferred. Conversely, for simpler parts made from low-melting-point alloys like zinc. Hot chamber die casting may offer a more efficient and cost-effective solution.
In summary, hot chamber and cold chamber die casting are two common. Techniques used in automotive manufacturing to produce high-quality metal parts. Each method has its advantages and limitations, influencing their suitability for different materials and applications.
5、Quality Control and Inspection Process Importance in Die Casting
Quality control is integral to the die casting process, as it directly impacts the performance. Reliability, and safety of the final products. By implementing rigorous quality control measures and inspection processes. Manufacturers can identify and rectify any defects or deviations early in the production cycle, minimizing waste and ensuring customer satisfaction.
5.1、Raw Material Inspection
The first step in quality control is inspecting the raw materials used in the die casting process. This includes verifying the quality and composition of the metal alloys. Checking for impurities or contaminants, and ensuring compliance with industry standards and specifications. Any discrepancies or deviations are addressed promptly to prevent issues during production.
5.2、Process Monitoring
During the die casting process, continuous monitoring is essential to maintain consistent quality and performance. This involves monitoring key process parameters such as temperature, pressure, and cycle times to ensure optimal conditions for casting. Advanced monitoring systems and sensors help detect any abnormalities or variations, allowing for timely adjustments and corrective actions.
5.3、Finished Product Inspection
Once the parts are cast and finished, thorough inspection is conducted to verify their quality and integrity. This includes dimensional inspection to ensure accurate dimensions and tolerances, visual inspection for surface defects or imperfections. Any non-conformities are documented and addressed according to established quality procedures.
5.4、Importance of Quality Control
Effective quality control is essential for ensuring product consistency, reliability, and customer satisfaction. By implementing robust quality control measures and inspection processes, manufacturers can:
Identify and mitigate potential defects or issues early in the production cycle
Minimize scrap, rework, and production downtime
Ensure compliance with industry standards and customer requirements
Enhance product performance, reliability, and longevity
Build trust and confidence with customers and stakeholders
By implementing comprehensive quality control measures and inspection processes, manufacturers can maintain product quality, consistency, and reliability.
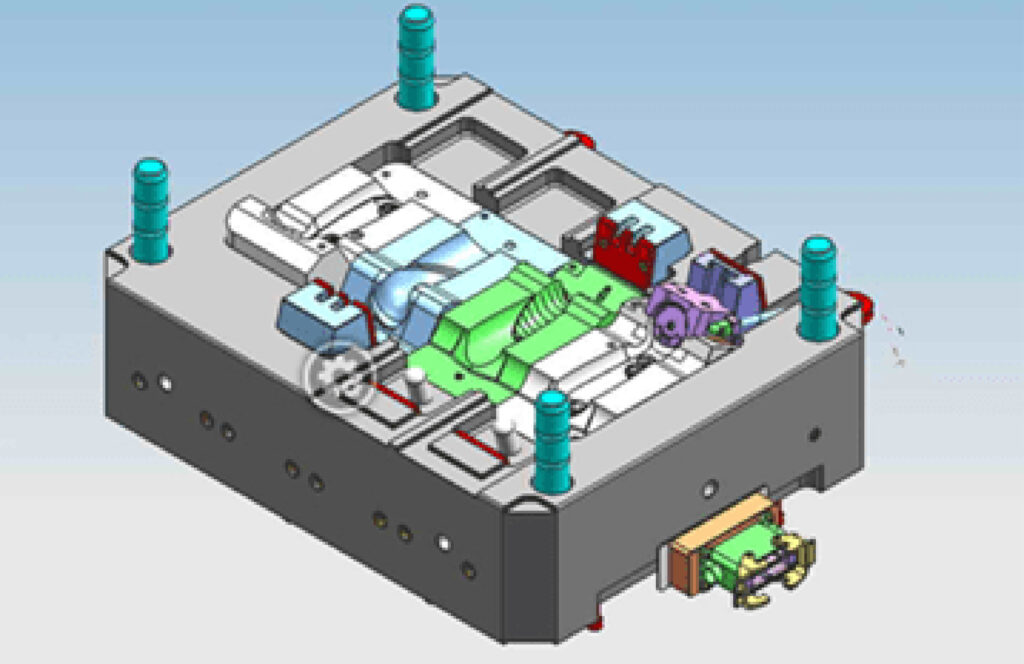
6、The Application of Digital Technology.
Digital technology plays a pivotal role in enhancing the efficiency and precision of the die casting process. From CAD/CAM design to simulation and intelligent manufacturin.Digital tools and techniques have revolutionized the way. Ddie casting operations are carried out, leading to improved quality, reduced lead times, and increased productivity.
6.1、CAD/CAM Design
Computer-aided design (CAD) and computer-aided manufacturing (CAM) software are essential tools in die casting design and production. CAD software allows engineers to create detailed 3D models of parts, molds, and tooling, facilitating precise design iterations and optimization. CAM software, on the other hand, enables seamless translation of design specifications into machine instruction. Streamlining the manufacturing process and minimizing errors.
6.2、Simulation and Virtual Prototyping
Simulation and virtual prototyping tools allow die casting manufacturers to evaluate and optimize the process before physical production begins. By simulating various casting scenarios, engineers can identify potential issues, such as porosity, shrinkage, or thermal stress, and make necessary.
Adjustments to improve part quality and production efficiency. Virtual prototyping enables rapid iteration and testing of design iterations, saving time and costs associated with traditional trial-and-error methods.
6.3、Intelligent Manufacturing
Intelligent manufacturing technologies, such as IoT sensors, data analytics, and machine learning. Are increasingly being integrated into die casting operations to enable real-time monitoring and optimization.
IoT sensors collect data on process parameters, machine performance, and product quality. Allowing for proactive maintenance, predictive analytics, and continuous process improvement. Machine learning algorithms analyze data to identify patterns, anomalies, and opportunities for optimization, enabling more efficient and adaptive manufacturing processes.
CAD/CAM design tools enable precise modeling and optimization of parts and tooling, while simulation and virtual prototyping tools. Allow for early identification and resolution of issues.
Intelligent manufacturing technologies enable real-time monitoring, analysis. And optimization of the production process, leading to improved quality, reduced lead times, and increased productivity.
7、Die Casting Applications in Automotive Suspension or Engine Component Parts
We rely on die casting for the production of critical components used in suspension and engine systems. Die casting offers advantages such as high precision, excellent surface finish, and dimensional stability. Making it an ideal choice for manufacturing components that require tight tolerances and intricate geometries.
7.1、Steering Knuckles
Steering knuckles, also known as steering arms or spindle supports, are key components of the steering system in vehicles. These components connect the wheel hubs to the suspension system and allow for the movement. Die casting is commonly used to manufacture steering knuckles due to produce complex shapes with high precision and strength.
7.2、Suspension Arms
Suspension arms, also referred to as control arms or A-arms, are critical components of the vehicle’s suspension system. These arms connect the chassis to the wheel hub assembly. And play a vital role in controlling the movement and alignment of the wheels.
Die casting is widely employed in the production of suspension arms to achieve the required strength.Stiffness. And dimensional accuracy while minimizing weight.
7.3、Cylinder Blocks
Cylinder blocks are the foundation of the engine, housing the cylinders, pistons, and other crucial components of the combustion process. Die casting is commonly used to manufacture cylinder blocks due to its ability to produce complex internal geometries. Intricate cooling passages with high precision and repeatability.
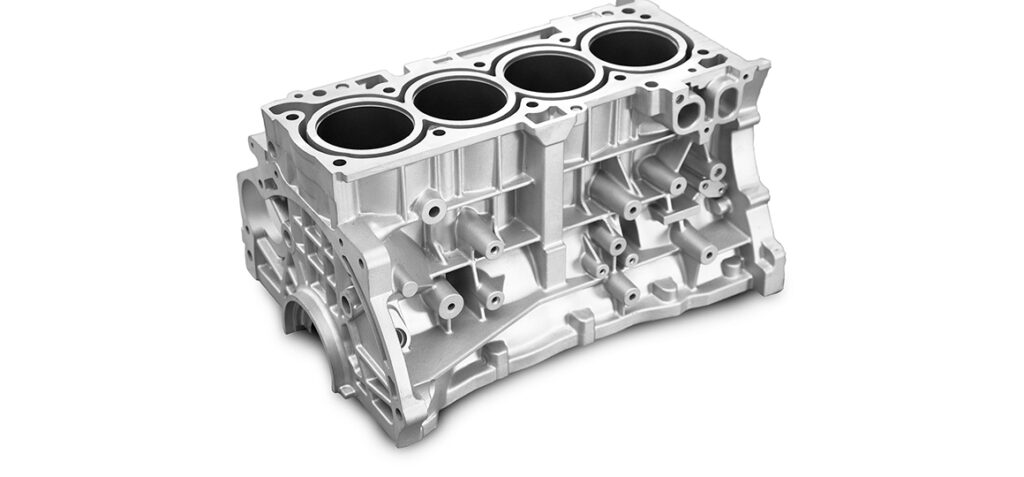
7.4、Other Applications
In addition to steering knuckles, suspension arms, and cylinder blocks. Die casting finds applications in various other automotive components, including transmission cases, differential housings, engine brackets, and more.
The versatility and efficiency of die casting make it an indispensable manufacturing process for producing. A wide range of automotive parts.
Conclusion
In conclusion, the die casting process stands as a cornerstone in modern manufacturing. Offering unparalleled precision and efficiency across various industries. From automotive components to aerospace parts and beyond, die casting’s versatility and reliability make it indispensable in today’s production landscape. By understanding its principles and embracing its applications, we unlock a world of possibilities for enhanced productivity. Cost-effectiveness, and the fabrication of intricate components. As we move forward, let us continue to explore and innovate within the realm of die casting. Driving progress and excellence in manufacturing.