News
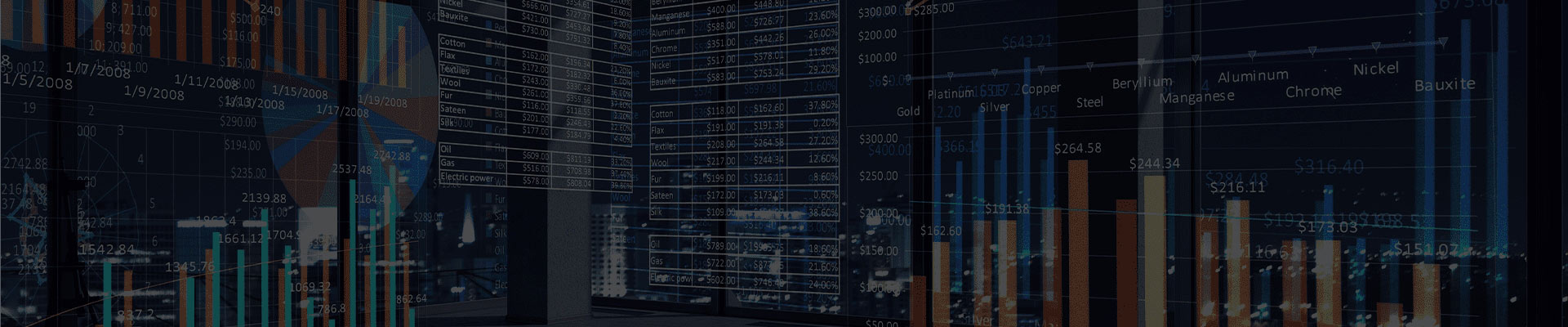
Contact Us
Complete control over products allows us to ensure our customers receive the best quality prices and
service
INQUIRY FORM
After years of devepopment, the company's welding technology mainnly includes gas shielded welding,
arc welding, laser welding and kinds of welding technologies, combined with automatic assemble
lines, through Ultrasonic Testing (UT), Radiographic Testing(RT), Magnetic particle Testing(MT)
Penetrant Testing(PT), Eddy Current Testing(ET), Pull-off force of testing, to achieve high
capacity, high quality and safer welding assemblies, we could supply CAE, MOLDING and 24-hour quick
quotation to provide customers with better service for chassis stamping parts and maching parts.
- Various automotive accessories
- Over 12 years of experience in mechanical processing
- Achieve strict precision machining and tolerances
- Consistency between quality and process
- Can achieve customized services
- On time delivery