The Importance of Precision in Metal Stamping: Enhancing Quality and Performance
Introduction:
Metal stamping is a critical process in manufacturing. It is particularly essential for industries requiring high-precision components such as automotive, aerospace, and electronics. The importance of precision in metal stamping cannot be overstated. Precision directly influences the quality, functionality, and performance of the final product. In this blog, we will discuss the key role of precision in the stamping process. We will also explore how it affects the overall outcomes.
Understanding Metal Stamping and Precision
Metal stamping is a manufacturing process where metal sheets are shaped into specific forms. This is done using dies and high-pressure presses. The process can involve various operations such as blanking, punching, bending, and embossing. Refers to the exactness and accuracy with which these operations are performed. This ensures that the components meet the required specifications and tolerances.
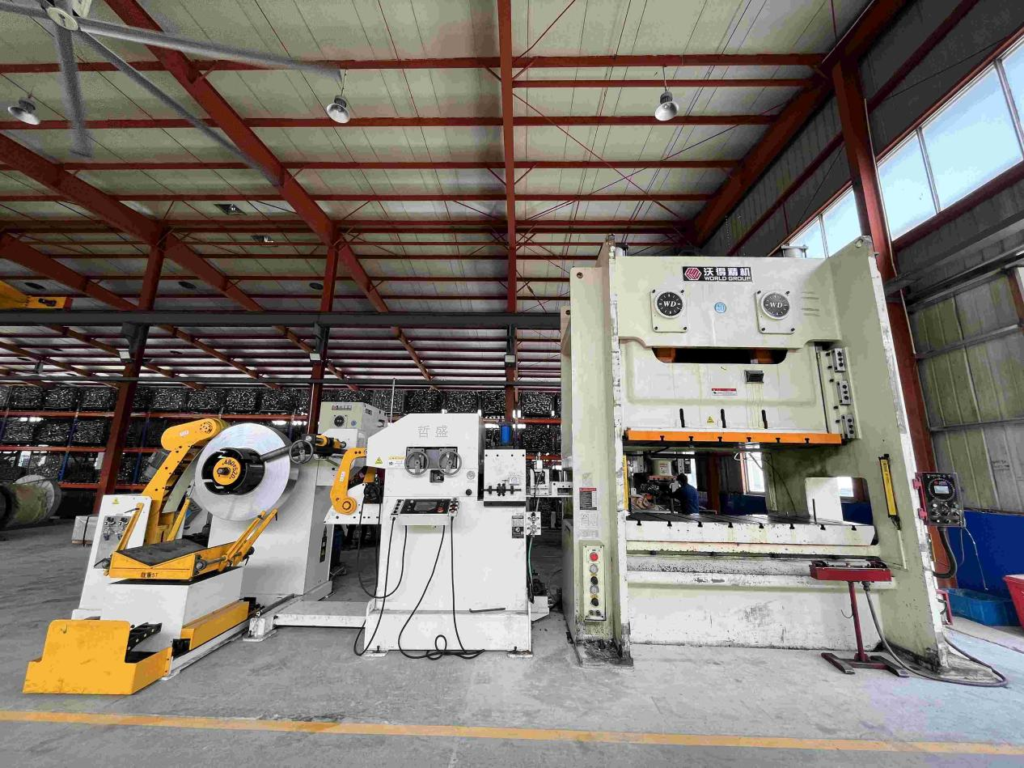
The Critical Role of Precision in Metal Stamping
Dimensional Accuracy
Precision in metal stamping ensures that each part produced is of the exact dimensions as specified. This is crucial for components that must fit together precisely in assemblies. Even a small deviation in dimensions can lead to misalignment, poor fit, or failure in the assembly process. Rectifying such issues can be costly.
Consistency and Repeatability
High precision in stamping processes guarantees that each part produced is identical to the others.
Consistency is vital for mass production, where large volumes of parts are manufactured.
Repeatable precision ensures that every piece performs uniformly.
This maintains the quality and reliability of the final product.
Material Efficiency
Precision in metal stamping optimizes material usage by reducing waste. Accurate cuts and shapes mean less scrap material. This leads to cost savings and more efficient use of raw materials. Efficiency is particularly important when working with expensive metals or large-scale production runs.
Enhanced Product Performance
The performance of a stamped metal component is often directly linked to its precision. In automotive applications, precision-stamped parts contribute to the overall safety and efficiency of the vehicle. In electronics, precise components ensure proper function and reliability of devices.
Quality Assurance
Precision is a key factor in quality control.
Adhering to tight tolerances and exact specifications minimizes the risk of defects and non-conformities.
This level of quality assurance is essential for maintaining customer satisfaction.
It also helps in meeting industry standards and regulations.
How Precision is Achieved in Metal Stamping
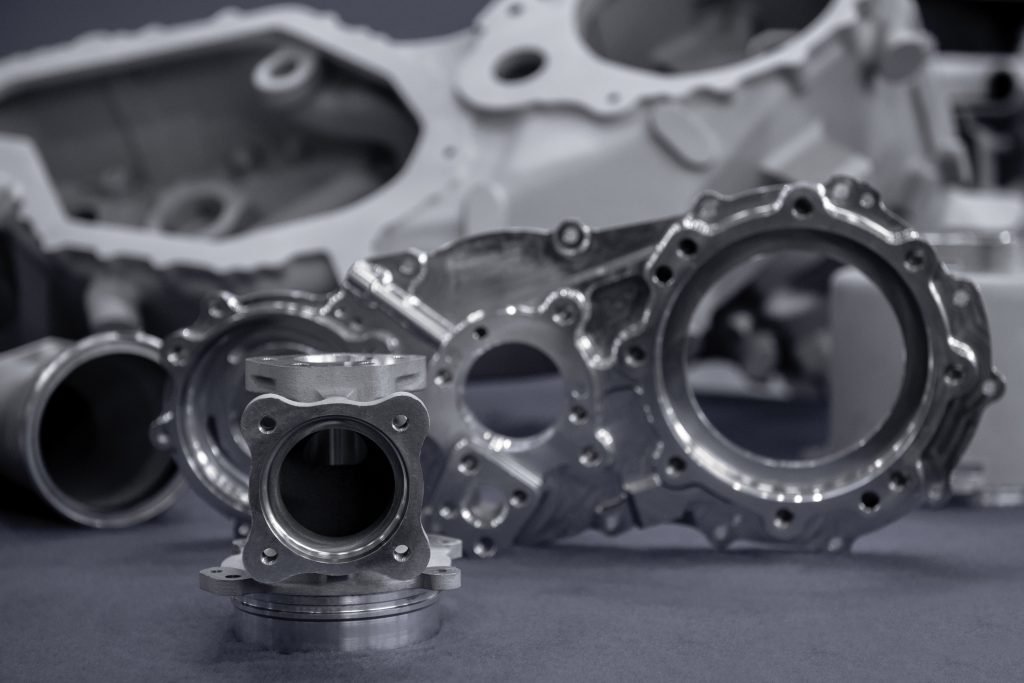
Advanced Tooling and Dies
The quality of the dies used in metal stamping is paramount to achieving highprecision.
Dies must be designed and manufactured to exact specifications using high-quality materials and advanced machining techniques.
Regular maintenance and calibration of dies also ensure continued precision.
Modern Press Technology
Utilizing modern stamping presses equipped with advanced control systems helps achieve high precision.
These presses offer greater control over parameters such as pressure, speed, and positioning.
This allows for more accurate and consistent operations.
Material Selection
The choice of material plays a significant role in the precision of stamped parts.
Materials with consistent thickness, hardness, and other properties are easier to stamp accurately.
Working with high-quality raw materials reduces the variability in the stamping process.
Precision Measurement and Inspection
Implementing precise measurement and inspection techniques throughout the stamping process ensures that parts meet the required specifications.
Using tools such as coordinate measuring machines (CMMs), laser scanners, and optical comparators helps in detecting any deviations early in the process.
Skilled Workforce
The expertise of the workforce involved in the metal stamping process cannot be overlooked.
Skilled operators and technicians who understand the nuances of precision stamping can make necessary adjustments.
They can also troubleshoot issues effectively, ensuring consistent quality.
Impact of Precision on Final Product Quality and Performance
Reliability and Durability
Precision-stamped parts contribute to the overall reliability and durability of the final product.
Components that are manufactured to exact specifications are less likely to fail or cause issues in operation.
This enhances the longevity and performance of the product.
1.Aesthetic and Functional Quality
Precision ensures that stamped parts not only function correctly but also meet aesthetic standards.
Clean cuts, smooth edges, and exact shapes are essential for parts that are visible or play a critical role in the product’s functionality.
Cost-Effectiveness
Achieving high precision may involve upfront investments in advanced equipment and tooling.
However, it leads to cost savings in the long run.
Reduced material waste, fewer defects, and less rework all contribute to a more cost-effective production process.
Compliance and Certification
Many industries have stringent standards and regulations that products must meet.
Precision in metal stamping helps ensure compliance with these standards.
This is necessary for certification and market approval.
Compliance is particularly important in industries such as automotive and aerospace, where safety and performance are critical.
Conclusion:
In metal stamping, precision is not just a desirable attribute; it is a necessity.
The role of precision extends from ensuring dimensional accuracy and consistency to enhancing material efficiency and product performance.
By employing advanced tooling, modern press technology, precise measurement techniques, and a skilled workforce, manufacturers can achieve the high levels of precision required to produce high-quality stamped components.
Ultimately,leads to reliable, durable, and cost-effective products that meet stringent industry standards and customer expectations.