Mastering the Craft Phosphating: Exploring Shao Yi’s Expertise Surface Treatment Phosphating
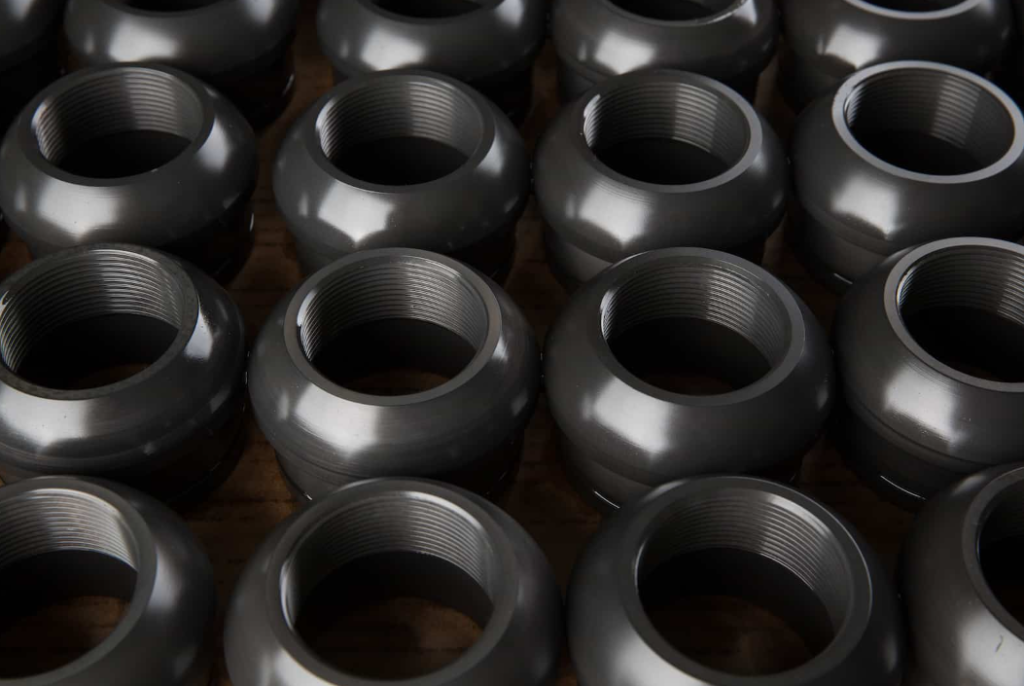
Introduction:
In the intricate world of automotive metal components, the quest for durability, corrosion resistance, and enhanced performance leads manufacturers to delve deep into the realm of surface treatments. Among the arsenal of techniques, phosphating stands out as a timetested and highly effective method. Shao Yi, a leader in automotive metal component manufacturing, has elevated the art of phosphating to new heights. In this extensive blog, we embark on a comprehensive journey to unravel the intricacies of phosphating, exploring its significance, the phosphating process, and how Shao Yi’s expertise in this domain contributes to superior quality in automotive components.
1. Understanding Phosphating: The Foundation of Surface Enhancement:
a. What is Phosphating?
Phosphating is a surface treatment process that involves the deposition of a phosphate coating on metal surfaces. Typically applied to steel components, this method enhances corrosion resistance, promotes paint adhesion, and provides a robust foundation for subsequent surface treatments.
b. The Significance of Phosphating:
In the automotive manufacturing industry, the selection of surface treatment technology is crucial for improving the performance and durability of components. Phosphating treatment, as a common and effective surface treatment method, plays a crucial role in the production of automotive components. The following are several aspects of the importance of phosphating treatment in automotive component manufacturing:
Improved corrosion resistance:
Phosphating treatment significantly improves the corrosion resistance of components by forming a phosphide layer on the metal surface. During the use of automobiles, especially in the face of adverse weather and road conditions, components are susceptible to corrosion. The parts that have undergone phosphating treatment can effectively resist corrosive environments such as moisture and salt spray, extending the service life of the parts.
Improvement of coating adhesion:
Phosphating treatment provides an ideal foundation for subsequent painting. The phosphating layer forms a micro concave convex structure on the metal surface, improving the adhesion between the coating and the metal surface. This not only ensures the firmness of the coating, but also improves the appearance quality of the components.
Reduce wear and friction:
Some special types of phosphating treatments, such as zinc phosphating, can significantly improve the wear resistance of components. This is of great significance for automotive components, especially in high friction areas such as engines and transmission systems. Phosphating treatment can help extend the service life of components by reducing their wear and tear.
Improving lubrication effect:
Some phosphating methods can also form phosphating coatings on the surface, improving the lubrication performance of components. This is crucial for some automotive components that require good lubrication between moving parts, such as engine components and transmission systems.
Improving the overall quality of components:
Phosphating treatment is not only a protective film on the metal surface, but also an improvement in the overall quality of the components. The parts treated with phosphating have been comprehensively improved in terms of corrosion resistance, mechanical properties, surface quality, etc., making them more reliable and superior automotive parts.
Adapt to diverse application needs:
There are various types of phosphating treatments, such as zinc phosphating, manganese phosphating, and iron phosphating. Each type of phosphating treatment can be selected based on the specific use and application environment of the components. This diversity makes phosphating an ideal choice to meet the needs of different automotive components.
Meet environmental requirements:
Modern phosphating methods are increasingly emphasizing environmental protection. Compared to some traditional surface treatment methods, phosphating treatment usually uses environmentally friendly chemical agents, and the waste generated during the treatment process can be treated reasonably, reducing the impact on the environment.
Overall, the importance of phosphating treatment in automotive component production is not only reflected in improving the performance and durability of components, but also in providing a reliable, economical, and environmentally friendly surface treatment solution for the automotive manufacturing industry. In this field, Shaoyi Company provides highquality phosphating treatment services for the automotive industry with its professional technology and advanced equipment, providing critical support for the safety, reliability, and lifespan of automobiles.
2. The Phosphating Process: A Symphony of Chemical Reactions:
a. Preparation of Metal Surface:
The phosphating process commences with the preparation of the metal surface. Shao Yi’s meticulous surface preparation involves thorough cleaning and degreasing to ensure that the substrate is free from contaminants that may impede the formation of a uniform phosphate coating.
b. Chemical Bath Immersion:
The prepared metal components are immersed in a chemical bath containing phosphoric acid and other proprietary additives. This bath triggers a series of chemical reactions that result in the formation of a crystalline phosphate coating on the metal surface.
c. Formation of Phosphate Coating:
During the immersion, the phosphoric acid reacts with the metal substrate, creating a layer of insoluble crystalline phosphates. This coating acts as a protective barrier, enhancing the metal’s resistance to corrosion and providing an ideal surface for subsequent treatments.
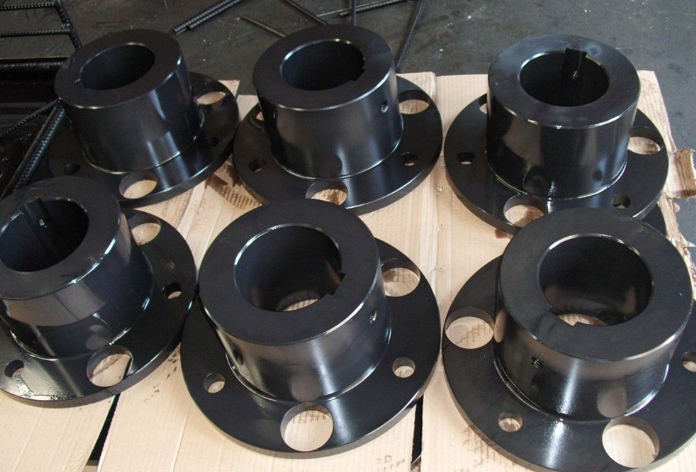
d. Rinsing and Drying:
Following the chemical reaction, the components undergo thorough rinsing to remove excess chemicals. Subsequently, the treated components are carefully dried to ensure the uniformity and adhesion of the phosphate coating.
3. Types of Phospha ting: Tailoring Solutions for Automotive Excellence:
a. Zinc Phosphating:
Zinc phosphating is a common variation, especially favored in the automotive industry. This type of phosphating not only provides corrosion resistance but also serves as an excellent base for subsequent painting processes, contributing to the longevity and aesthetics of automotive components.
b. Manganese Phosphating:
Manganese phosphating, with its enhanced wear resistance properties, finds applications in components exposed to highstress environments. Shao Yi’s expertise in tailoring phosphating solutions ensures that the choice of phosphating type aligns with the specific requirements of each automotive component.
c. Iron Phosphating:
Iron phosphating is known for its versatility and costeffectiveness. Shao Yi strategically employs iron phosphating in components where a robust foundation for paint adhesion and corrosion resistance is essential, ensuring optimal performance and longevity.
4. Advantages of Phosphating: Elevating Automotive Components to Excellence:
a. Corrosion Resistance:
The primary advantage of phosphating is its ability to impart corrosion resistance to metal components. Shao Yi’s phosphating expertise ensures that our automotive components withstand harsh environmental conditions, contributing to the longevity of vehicles.
b. Paint Adhesion:
Phosphating acts as a key facilitator for paint adhesion. Shao Yi’s precision in phosphating processes ensures that the phosphate coating provides an ideal surface for subsequent painting, resulting in a durable and aesthetically pleasing finish.
c. Improved Lubrication:
Certain phosphating variations contribute to improved lubrication properties. This is particularly beneficial in automotive applications where components undergo friction and wear, enhancing the overall performance and efficiency of the vehicle.
d. Wear Resistance:
Phosphating, when tailored appropriately, enhances wear resistance in components subject to mechanical stress. Shao Yi’s application of phosphating techniques ensures that our components maintain their integrity and functionality under demanding operational conditions.
5. Shao Yi’s Expertise in Phosphating: Pioneering Excellence in Automotive Components:
a. StateoftheArt Facilities:
Shao Yi boasts stateoftheart facilities equipped with cuttingedge phosphating equipment. Our commitment to excellence is reflected in the sophistication of our phosphating processes, ensuring precision, uniformity, and adherence to the highest industry standards.
b. Customized Solutions:
Recognizing the diverse applications of automotive components, Shao Yi offers customized phosphating solutions. Our expert technicians assess the specific requirements of each component and tailor the phosphating process accordingly, guaranteeing optimal performance and longevity.
c. Quality Control Measures:
Quality control is paramount in Shao Yi’s phosphating processes. Rigorous inspections and testing protocols are implemented to verify the thickness, adhesion, and uniformity of the phosphate coating, ensuring that each component meets or exceeds stringent quality benchmarks.
d. Environmental Responsibility:
Shao Yi places a strong emphasis on environmental responsibility in its phosphating processes. Effluent treatment systems and ecofriendly formulations are integrated into our operations, aligning with our commitment to sustainable and responsible manufacturing practices.
6. Innovation in Phosphating: Shaping the Future of Automotive Excellence:
a. NanoPhosphating Technologies:
Shao Yi is at the forefront of innovation in phosphating technologies. The exploration of nanophosphating techniques is underway, promising even greater precision, enhanced properties, and reduced environmental impact, shaping the future of automotive surface treatments.
b. Integration with Digital Management:
The integration of phosphating processes with digital management systems at Shao Yi enhances control, monitoring, and traceability. This synergy ensures that each component undergoes phosphating with the utmost precision, contributing to a seamless and digitally optimized manufacturing ecosystem.
7. Educational Initiatives: Empowering the Industry with Knowledge:
a. Training Programs:
Shao Yi is committed to knowledge sharing. We conduct training programs and workshops, both internally and externally, to disseminate information about phosphating processes. By empowering industry professionals with knowledge, we contribute to the advancement of surface treatment practices across the automotive sector.
b. Collaboration with Educational Institutions:
Shao Yi collaborates with educational institutions to foster research and development in surface treatment technologies. By engaging with academic partners, we contribute to the evolution of phosphating methodologies and the exploration of new frontiers in automotive surface enhancements.
8. Conclusion: Shao Yi’s Phosphating Excellence A Testament to Automotive Ingenuity:
In the intricate tapestry of automotive manufacturing, where longevity, performance, and aesthetics converge, Shao Yi’s expertise in phosphating emerges as a shining thread. The commitment to precision, customization, and innovation positions us as pioneers in the realm of surface treatment. As we continue to refine our phosphating processes and explore new horizons, Shao Yi remains dedicated to shaping the future of automotive excellence, one meticulously phosphated component at a time. Our story is one of mastery, innovation, and an unwavering commitment to setting new standards in the automotive industry.
Are you in search of a trusted partner for precision-crafted automotive metal components? Look no further! Contact Shao Yi, we specialize in the customization and manufacturing of high-quality metal parts that meet the exacting standards of the automotive industry.