Unveiling Precision: Shaoyi’s Comprehensive PPAP Process
INTRODUCTION
In modern automotive manufacturing, every detail is crucial, whether it is driver safety or vehicle performance. Therefore, ensuring the quality of automotive components cannot be overlooked. In order to achieve the highest quality standards, we use the PPAP process, or the “Production Part Approval Process”. This is a comprehensive quality control and verification system designed to ensure that our automotive parts meet customer needs and industry standards. In this blog, we’ll take an in-depth look at our company’s PPAP process, highlighting our commitment to quality and how we ensure that every detail receives precise attention.
Understanding the PPAP Process
First, let’s understand what PPAP stands for; Production Part Approval Process. This process is a globally recognized quality management system standard designed specifically for the automotive industry. It is based on the ISO 9001 standard with additional requirements specific to the automotive industry. The PPAP process defines a quality management system that helps an organization consistently meet customer and regulatory requirements.
Importance of PPAP Process
The PPAP process is of critical importance in the automotive manufacturing industry for the following reasons:
Strict Quality Standards: The PPAP process sets strict quality standards that automotive component manufacturers are required to adhere to. This includes a range of criteria from design and production to customer satisfaction and continuous improvement, ensuring that every aspect of the manufacturing process is quality-oriented.
Global Recognition: PPAP is a globally recognized standard. This means that certified companies can offer their products to automotive manufacturers worldwide, tapping into international markets and opportunities. It provides a common language for quality assurance in the automotive industry.
Reduced Defects: Implementing a PPAP process reduces defects and ensures that products consistently meet or exceed customer expectations. This results in fewer recalls and warranty claims, saving automakers money and preserving their reputations.
Increased Efficiency: PPAP focuses on process efficiency and waste reduction. This not only saves money but also promotes environmentally-friendly manufacturing practices, combining quality with sustainability, a growing concern in the automotive industry.
Customer Confidence: PPAP certification gives customers and partners confidence. It demonstrates a company’s commitment to providing high quality products and continuously improving its processes. It symbolizes a company’s commitment to upholding the highest quality standards.
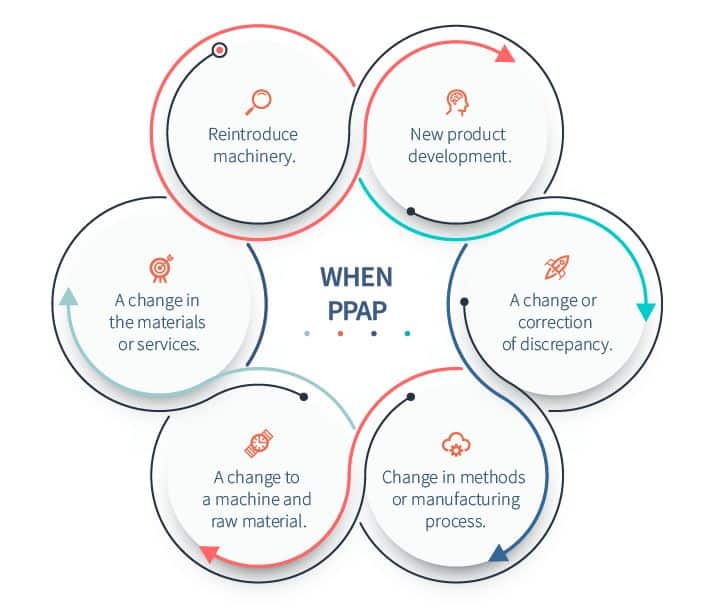
Shaoyi’s PPAP Process
At Shaoyi, the PPAP process is key to ensuring high quality automotive parts. Below are key aspects of our PPAP process:
Documentation Submission: Our PPAP journey begins with the preparation and submission of all necessary documentation, including design documents, process flow diagrams, control plans, Failure Mode and Effects Analyses (FMEA), and more.
Sample Evaluation: Once the documentation is approved, we build samples and conduct a thorough evaluation. This includes measurement, testing, verification of design specifications and performance requirements, etc.
Approval and Production: Once the samples have passed the evaluation, we obtain customer approval and begin full production. However, the PPAP process doesn’t stop there, as we continue to monitor and measure production parts to ensure consistent quality.
Continuous Improvement: Our PPAP process is not just a one-time event. We continually evaluate and improve our manufacturing process to ensure that the quality of our parts is always of the highest standard.
The PPAP Process Journey
Achieving and maintaining PPAP certification is no small task. It requires careful planning, execution and ongoing monitoring. Here are the key steps it involves:
1. Gap Analysis: Typically, the first step we take to begin this journey is to conduct a gap analysis. This involves a comprehensive review of our existing quality management system to determine consistency with PPAP and areas for improvement.
2. Training: We ensure that all employees are trained on the requirements of PPAP and the importance of quality management. This training covers all levels of our organization, from the production floor to top management.
3. Process Improvement: Focusing on continuous improvement, we systematically review and improve our manufacturing processes. This includes all aspects from design and development to production, testing and delivery. Each process is analyzed to ensure that it is optimized for quality.
4. Documentation: Thorough documentation is the foundation of PPAP certification. We carefully document our processes, procedures and quality control measures. These documents not only demonstrate our compliance, but also provide a valuable resource for continuous improvement.
5. Internal Audits: We conduct periodic internal audits to ensure that our quality management system is functioning as intended. These audits help to identify areas for improvement and take corrective action where necessary.
6. External Certification Audits: Once we are confident of our compliance, an external certification body conducts a rigorous audit. This audit compares our quality management system to the requirements of PPAP. Being certified is proof of our commitment to quality.
Customer Satisfaction and the PPAP Process
The PPAP process not only helps to ensure the quality of our parts, but also has a direct impact on customer satisfaction. Customers can rest assured knowing that our products have been rigorously verified and approved to meet their needs. This not only increases customer trust, but also helps build long-term relationships.
In the highly competitive automotive manufacturing industry, precision and reliability are key elements that we cannot afford to ignore. Through our company’s PPAP process, we not only ensure the quality of our parts but also promise that every detail is given precise attention. The PPAP process is a symbol of our relentless pursuit of quality as we provide our customers with the highest quality automotive components.
As the future unfolds, we will continue to push the boundaries of quality, efficiency and sustainability. Through our strong commitment to PPAP and dedication to continuous improvement, we are not only shaping the quality of automotive parts but also the future of automotive manufacturing. We thank you for joining us on our PPAP process journey, a journey where every detail is critical, and precision is our promise.
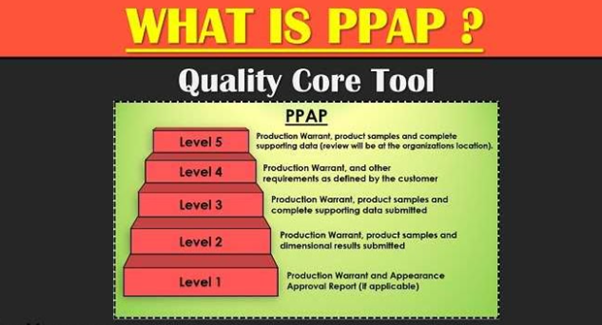
Conclusion
In the highly competitive automotive manufacturing industry, where quality is not something to be compromised, the PPAP process is the gold standard for ensuring that automotive components meet the highest quality standards. Our company’s commitment to achieving and maintaining this certification sets us apart. It symbolizes our commitment to delivering products that not only meet but exceed industry standards, providing our customers with the confidence they need in their supply chain.
With PPAP as our guiding principle, we will continue to drive innovation and excellence in the automotive parts industry. Our goal is not just to provide automotive parts, but to provide our customers with the peace of mind of knowing that every part we provide is of the highest quality and meets the most stringent standards.
As we look to the future, we remain committed to pushing the boundaries of quality, efficiency and sustainability. Through our strong commitment to PPAP and dedication to continuous improvement, we are not only shaping the quality of automotive parts, but the future of automotive manufacturing to be safer, more reliable and superior. Thank you for joining us on our journey through the PPAP process, where every detail is critical and precision is our promise.